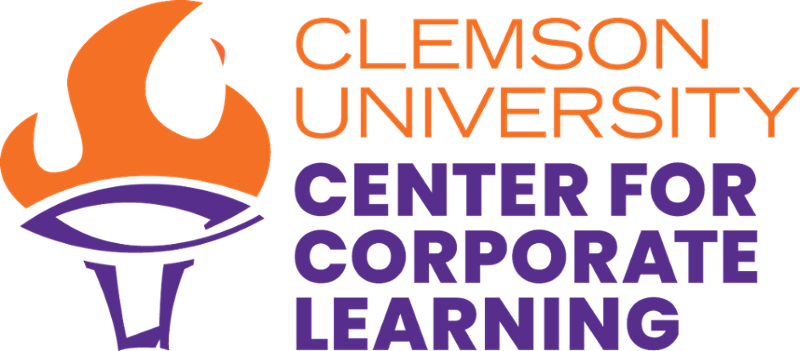
Maintenance Management Certification
Earn The Respect Of Your Employer And Colleagues With A Maintenance Management Certification. Register Now For Clemson University Maintenance Management Certification Classes
Maintenance managers who build their skill set through training offer a competitive edge to an organization. Shrewd maintenance managers know how to anticipate and avoid costly problems, making operations more efficient, productive, and profitable.
Clemson University Center for Corporate Learning, working with Life Cycle Institute, is offering maintenance management professionals the opportunity to achieve their Maintenance Management Certification through one of the country's most respected engineering schools.
Your Organization Will Applaud Your New Skills
Gain immediate dividends because you can instantly apply to your job the practical skills you will learn. You'll also demonstrate your commitment to building a solid maintenance program. This means you'll become more valuable to your organization.
You will discover how to:
- Build and sustain a maintenance program.
- Establish appropriate maintenance KPIs and visual management dashboard.
- Select the optimum equipment maintenance strategy.
- Meet your production goals and maintain your valuable assets.
- Select the optimum equipment maintenance strategy.
- Implement work management strategies that improve asset availability and utilization.
- Increase maintenance personnel productivity.
- Build a problem-solving culture.
- Manage an effective maintenance budget.
To earn a Maintenance Management Certification, candidates must complete four courses (at least two of them in Greenville, the rest in Charleston) and successfully pass the Maintenance Management Certification exam within three years.
Program Details
Per Course: $1995
MMC Exam: $295
Total investment: $8275
CEUs: 8.4
Required Courses
-
Maintenance Management Skills
Maintenance Management Skills teaches supervisors how to lead a world-class maintenance department using planning and scheduling best practices to drive work execution, and motivational and time-management techniques to improve maintenance worker productivity. The result is improved staff motivation, lower employee turnover, increased output and reduced waste of resources.
Participants will build an action plan for managing their human capital while developing an effective program for managing assets. Supervisors will learn how to leverage their personal supervisory style, apply time management techniques, run effective meetings and improve maintenance delivery. Explore how to make the transition from a technician to a supervisor and investigate common supervisory staffing issues like supervising friends, orienting new employees and delegating responsibility when necessary.
The course uses case studies, group discussion, reflection activities and exercises to help you apply what you learn to your work situation.
In This Training, Learn How To:
- List the roles, goals and motivation of a Maintenance Supervisor
- Describe maintenance management critical success factors:
a) Using planning and scheduling to drive work execution
b) Techniques to improve worker productivity
c) Managing meetings effectively - Practice techniques to effectively manage people:
a) Methods to handle problems with employees, vendors, coworkers
b) Decision making
c) Smart delegation
d) Supervisory staffing issues: orientation, discipline, supervising friends, and substance abuse issues - Build a management skills action plan:
a) Assess your supervisory style to identify strengths and areas for development
b) Apply time management techniques
c) List ways to control reactions and make good decisions in times of stress
d) Outline ways to make the change from technician to supervisor - Outline an effective program to manage your assets
a) Best practices for applying preventive maintenance, predictive and condition-based technologies
b) Guidelines for assessing your existing PM system and making improvements
Who Should Attend Training
This course is designed for maintenance managers and supervisors. Ideal candidates either supervise maintenance workers or manage maintenance through supervisors. This course is also recommended for people looking to improve their skills or those being considered for advancement. Supervision from other related areas such as Operations, Warehouse and Housekeeping are also invited.
Additional Information
Each course includes a comprehensive active learning manual, morning and afternoon refreshments, lunch, and the use of a fully equipped e-business center. Class hours are 8:30 a.m.-4:30 p.m., Tuesday through Thursday. All students completing a class at the Life Cycle Institute will receive a certificate of completion awarding 2.1 CEUs.
-
Managing Planning and Scheduling
In Managing Planning and Scheduling, participants build a work management program based on Reliability Excellence best practices. The course is designed for a Lead Planner or Department Manager to establish a proactive work management program or to transform an existing program into an effective, results-producing department that positively impacts maintenance costs, plant reliability measures and employee morale.
Managing Planning and Scheduling examines topics like designing a work management program strategy, developing standard processes and work, establishing program measures, managing staff development, and planning program improvement. Learners will walk away with a solid foundation for an effective maintenance work management program.
Learn How To:
- Explain the business case for proactive work management
- Build a work management process flow chart and responsibility matrix
- Draft a work management program strategy: objectives, key performance measures, targets, reporting and monitoring methods
- Develop governing principles and standard procedures for CMMS data entry and use
- Outline a management of change process for job plans
- Describe a disciplined approach to managing work for a planned shutdown
- Scoping and validating work, project management, communication, reviews, lessons learned
- Develop an implementation plan to establish or transform a planning program, including:
- Establishing program standards and templates
- Incorporating visual management into your program
- Job performance feedback and continuous improvement
- Backlog management
- Managing the people side of change (change management)
- Develop an audit and continuous improvement strategy for the planning program
- How trends in manufacturing and technology impact planning/scheduling
- How the planner interacts with failure data and root cause analysis efforts
- How equipment criticality and risk management influence maintenance strategy
- Build performance management and development strategies for planning personnel
Who Should Attend
People in the following roles should participate in this training:
- Lead and senior planners
- Planning Department Managers
- Maintenance Managers
- Reliability Change Agents
- Reliability Managers
- Continuous Improvement Managers
Additional Information
Each course includes a comprehensive active learning manual, morning and afternoon refreshments, lunch, and the use of a fully equipped e-business center. All students completing a class at the Life Cycle Institute will receive a certificate of completion awarding CEUs. Class hours are 8:30 a.m.-4:30 p.m., Tuesday through Thursday.
Elective Courses (Pick Two)
-
Maintenance Planning and Scheduling
Maintenance planning and scheduling is one of the fastest and most effective investments an organization can make to improve productivity and availability. The processes in this course pave the way for planning and control of maintenance resources. Equipment reliability is increased. Waiting times, unnecessary parts and inaccurate information are eliminated. Budgeting is easier and more accurate. Maintenance tasks are as much as 50% more efficient in terms of costs and time.
Maintenance Planning and Scheduling examines topics including a proactive work management process, job estimation and prioritization, backlog management, job plan development, work scheduling and coordination, tracking progress, and supporting reliability engineers with valuable equipment history and root cause analysis input.
In This Training, Learn How To:
- Outline a proactive work management process
- Calculate work management performance metrics
- Develop a comprehensive "standard" job plan
- Apply work planning best practices
- Identifying work and submitting work orders
- Prioritize work using equipment criticality (RIME)
- Backlog management
- Estimating work
- Effective job plans
- Job kitting
- Summarize requirements for work management support systems
- Equipment data and history
- Work order system
- Standard job plans and job libraries
- Bill of materials
- Technical library
- Build a schedule using best practices
- Master Schedule
- Schedule constraints
- Schedule balance and leveling
- Coordination meetings
- Develop key partnerships needed for effective maintenance planning and scheduling
- Differentiate maintenance types and how they impact the planning/scheduling efforts
Who Should Attend Training
Successful maintenance planning and scheduling programs require the disciplined application of proven processes and interdepartmental partnerships. It is important for departments that are influenced and impacted by the processes to understand the processes. People in the following roles should participate in this training:
- Maintenance Planner/Schedulers
- Production Supervisors
- Storeroom Managers
- Maintenance Managers
- Operation Coordinators
- Maintenance Supervisors
- Plant Engineers
Additional Information
Each course includes a comprehensive active learning manual, morning and afternoon refreshments, lunch, and the use of a fully equipped e-business center. Class hours are 8:30 a.m.-4:30 p.m., Tuesday through Thursday. Virtual course hours run from 11 a.m.-5 p.m. EST. All students completing a class at the Life Cycle Institute will receive a certificate of completion awarding 2.1 CEUs.
-
Materials Management
Managing a storeroom is a balancing act. Storeroom managers must have the materials available to keep production flowing while minimizing inventory investment.
In this three-day class, you will learn how to ensure the right parts are in the right place at the right time. When you apply the knowledge and skills learned in this class, quality will increase, and costs will decrease. You will be able to manage your storeroom in a way that successfully balances the needs of operations and maintenance while optimizing your inventory and carrying costs.
In This Training, Learn How To:
- Discuss the materials management challenges that organizations are facing
- Identify the elements of materials management
- Discuss how Materials Management fits into the overall umbrella of Reliability Excellence
- Discover the characteristics and steps involved in effective materials management processes
- Discuss the basic steps involved in implementing effective Inventory Control best practices
- Summarize the basic steps involved in implementing effective Warehouse Management best practices
- Describe how a CMMS can support materials management processes and best practices
- Identify contributors to the total cost of materials
- Practice techniques to manage inventory investment
- Define the standard set of basic materials management key performance indicators
- Develop an (inventory/investment management processes) Action Plan
Who Should Attend Training
Anyone involved in materials—directly or indirectly—will find value in Materials Management, including:
- Materials Managers
- Maintenance Manager
- Purchasing
- Storeroom Personnel
- Planner/Schedulers
- Operations Managers
What Our Students Are Saying
"Facilitator was knowledgeable, engaging, fair and interesting. I've acquired a lot of knowledge that I will take back with me to improve inventory accuracy. I look forward to applying what was learned to our Memphis warehouse." - Eugene Fellows, Cargill
"The Life Cycle Institute facility was excellent for training. The staff was a pleasure to work with and the facilitator was one of the best instructors I have studied under. He provided excellent examples, hands-on material and real life feedback. My experience was over the top." - Gordon Vickous, Facility Supervisor, Berry Plastics
"I was a bit apprehensive about registering for the course but I'm so very glad that I did. The quality and amount of information covered definitely made my trip to Charleston worthwhile!" - John Nobel, Logistics/Facilities Management, University of Saskatchewan
Additional Information
Each course includes a comprehensive active learning manual, morning and afternoon refreshments, lunch, and the use of a fully equipped e-business center. Class hours are 8:30 a.m.-4:30 p.m., Tuesday through Thursday. All students completing a class at the Life Cycle Institute will receive a certificate of completion awarding CEUs.
-
Risk-Based Asset Management
Explore how to improve asset availability and meet reliability goals by applying a risk-based approach to asset maintenance and operations
Explore how to improve asset availability and meet reliability goals by applying a risk-based approach to asset maintenance and operations. In the Risk-Based Asset Management (RBAM®) course, you practice prioritizing reliability efforts on critical equipment and failures that impact your operation. RBAM incorporates reliability-centered maintenance (RCM) principles and continuous improvement practices like PDCA to position your program for decreased downtime, lower maintenance expenditures, and an acceptable total cost of ownership.
During the course, participants classify and analyze assets and failures to rank equipment criticality and draft a risk plan. Next, learners build a failure mode and effects analysis (FMEA) to define control strategies and populate an equipment maintenance plan. Group activities in the class include examining how life cycle cost influences investment and choosing key performance indicators to manage a reliability program. Specific emphasis will be placed on the resources needed to create an asset management plan – a risk, maintenance and asset operations plan – that can manage the entire life cycle of an asset.
Learn How To:
- Draft components of an asset management plan: risk and maintenance plan
- Describe what an asset management organization needs to know to manage risk and improve performance
- Describe the four phases in a risk-based asset management model
- List ways to extend the life of assets and evaluate their effectiveness
- Use a failure mode and effects analysis (FMEA) to analyze risks and map control strategies to failure modes
- Describe how audits, reviews and key performance indicators drive continuous improvement
- Practice applying a standard process for preventive maintenance optimization
- Select the optimal strategy for renewal or disposal based on asset management strategy
Who Should Attend
This is ideal for people responsible for the design, installation, commissioning, operation and maintenance of capital assets and auxiliary equipment. This includes project engineers, reliability engineers, maintenance managers, operations managers, and engineering technicians.
Additional Information
Each course includes a comprehensive active learning manual, morning and afternoon refreshments, lunch, and the use of a fully equipped e-business center. Class hours are 8:30 a.m.-4:30 p.m., Tuesday through Thursday. All students completing the class will receive a certificate of completion awarding 2.1 CEUs.
-
Root Cause Analysis
Armed with what you learn in this course, you will apply a process for root cause analysis, establish a culture of continuous improvement, and create a proactive environment. Learn to ask the right questions, establish triggers that drive you to the RCA process, and perform a cost-benefit analysis.
When you learn to practice true root cause analysis, you can eliminate the latent roots and stop recurring failures once and for all. After this three-day course, you can develop and implement an RCA program, thus leading your organization to reduced downtime, increased production and a more proactive culture.
Learn How To:
- Outline a 6-step root cause analysis process that promotes critical thinking, creative collaboration, countermeasure analysis and solution verification
- Explain how a robust root cause analysis program drives continuous improvement and business results
- Plan your RCA program:
- Outline triggers for RCA efforts based on business case thinking
- Define RCA roles and responsibilities
- Define program goals, measures and standards
- Select and apply a range of RCA tools to solve different problems:
- 5-why
- Design and application review
- Ishikawa (fishbone)
- Sequence of events
- Fault tree analysis
- Change analysis
- Events and causal factors
- FMEA
- List RCA group facilitation best practices
- Use an A3 tool to visually manage and track activities, report on and communicate RCA results
Who Should Attend
Anyone interested in acquiring or improving advanced problem-solving skills will benefit from this course. Individuals responsible for continuous improvement, solving maintenance and reliability problems and preventing future occurrences of equipment and system failures, including technicians, engineers, supervisors and managers.
Additional Information
Each course includes a comprehensive active learning manual, morning and afternoon refreshments, lunch, and the use of a fully equipped e-business center. Class hours are 8:30 a.m.-4:30 p.m., Tuesday through Thursday. All students completing a class at the Life Cycle Institute will receive a certificate of completion awarding 2.1 CEUs.
-
Predictive Maintenance Strategy
Make Data-driven Decisions and Improve Quality, Productivity and Profitability
Predictive maintenance (PdM) is not a tool, technique or certification. Predictive maintenance is a philosophy that uses the equipment's operating condition to make data-driven decisions and improve quality, productivity and profitability. Unlike industry courses that focus on applying specific technologies like vibration monitoring or oil analysis, this course focuses on establishing, managing and sustaining results from a comprehensive PdM program.
The Predictive Maintenance Strategy course considers predictive maintenance as a component of a larger asset management strategy to diagnose, prevent and postpone failures. During this three-day course, you will learn the theory and application of multiple PdM technologies. You will review critical success factors of results-producing PdM programs. Through group activities and case studies, you will determine which predictive technologies to use, how to set goals for your program, track progress and practice how to communicate results to different stakeholders. By the end of the session, you will have outlined what a successful PdM program can look like at your organization.
Learn How To:
- Explain how a combination of predictive maintenance, condition monitoring and non-destructive testing mitigates risk and optimizes your asset maintenance plan.
- Describe the theory, application and safety considerations of 5 PdM technologies
- Vibration analysis
- Thermography
- Tribology (oil analysis)
- Ultrasonics
- Motor circuit analysis
- Recognize visual inspection as a component of a PdM program
- Draft a predictive maintenance strategy that incorporates critical success factors in the following areas:
- Data and measurement requirements
- Planning and set-up
- Monitoring the program
- Showing results
- Compare your current PdM program to best practices and build a plan to meet your PdM goals
Who Should Attend
Maintenance Managers, PdM Managers, Maintenance professionals, continuing education students, and any person responsible for justifying or managing duties related to a PdM program.
Additional Information
Each course includes a comprehensive active learning manual, morning and afternoon refreshments, lunch, and the use of a fully equipped e-business center. Class hours are 8:30 a.m. to 4:30 p.m., Tuesday through Thursday. All students completing the class will receive a certificate of completion awarding 2.1 CEUs.
Registration
Course ScheduleCourse | Date | CEUs | Cost | |
---|---|---|---|---|
Maintenance Management Certification | See course schedule. | 8.4 | $1,995 per course $295 MMC Exam $8,275 Total Investment |
Register |
Maintenance Management Skills | See course schedule. (Charleston) | 2.1 | $1,995 | Register |
Managing Planning and Scheduling | 2.1 | $1,995 | Register | |
Maintenance Planning and Scheduling | See course schedule. (Charleston) | 2.1 | $1,995 | Register |
Materials Management | 2.1 | $1,995 | Register for Coursework | |
Risk-Based Asset Management | See course schedule. (Greenville) | 2.1 | $1,995 | Register for Exam |
Root Cause Analysis | See course schedule. (Virtual) | 2.1 | $1,995 | Register |
Predictive Maintenance Strategy | 2.1 | $1,995 | Register |
Live Virtual Classes
Virtual Instructor-Led Training (VILT) combines the benefits of traditional classroom training and online learning. It allows participants to experience live instructor-led training without going to a classroom or having the instructor present in person.
Using Zoom's technology, this video-based training allows learners to ask questions, participate in discussions, and get trained together, regardless of location. Participants in the Institute's virtual classes will learn the same content from the Institute's in-person classes while participating in professionally facilitated sessions with activities that stimulate participation and learning:
- Online breakout sessions with facilitator support
- Individual and group assignments and discussions
- Polls, Q&A, and online whiteboard activities that keep learners engaged
Life Cycle Institute's virtual classes were developed by industry-leading subject matter experts and certified professional instructional designers with experience converting live, instructor-led classes into engaging and effective online learning experiences using learning best practices.
The virtual classes will entitle participants to the same CEUs as in-person classes and will also count toward certification.